With this, Wrist-Klevenberg is taking the next step in the process of becoming more sustainable. Where previously the cooling and freezing installation operated on chemical refrigerants, it has now switched to a cooling and freezing installation that runs entirely on a natural refrigerant, CO2.
Wrist-Klevenberg
Despite the current corona crisis, the developments and innovations at Wrist-Klevenberg are not standing still. We have replaced the entire cooling and freezing system of Wrist-Klevenberg.
Combating climate change
By opting for a CO2 refrigeration and freezer installation, Wrist-Klevenberg is contributing to combating global warming. In principle, the chances of leakage in a closed installation are non-existent, but in the event of a calamity leading to a leak, the emissions are 4000 times less harmful for the environment than with chemical refrigerants.
Thanks to the comprehensive control system, it is possible to adapt the installation as efficiently as possible to the ambient temperatures. Thanks to the central computer, the installation is monitored 24 hours per day. It is also possible to manually monitor and adjust the installation remotely.
This benefits not only the environment, but the company as a whole. Wrist-Klevenberg can now continue to guarantee the quality of its products in a responsible manner. Now and in the future.
A long partnership
We have worked with Wrist-Klevenberg for many years. Our refrigeration and freezer systems are complete custom designs for our customers. We are currently the only one in the world to do this.
First, we map out the customer's wishes and then we create a design. All the components are matched to each other as optimally as possible. We also take other elements within the project into account. For example, we now also take care of technical work that is not directly related to refrigeration, such as realising a suitable floor.
Market leader
With the switch to natural refrigerants, Wrist-Klevenberg is a market leader. Despite the fact that the government has a strict policy to phase out chemical refrigerants, about 5% of the installations in the field currently run on natural refrigerants. This percentage is slightly higher for new buildings.
Smooth transition
Not only is the installation itself efficient, we also approach the phased process towards the assembly of the installation in such a way that the logistical process can continue to run at full capacity.
The current machines are now partly exposed to rain, as they are situated on the roof. The new machines will be placed on the side of the building. The pallets can remain where they are and the old installation will only be switched off once the new installation has been activated"
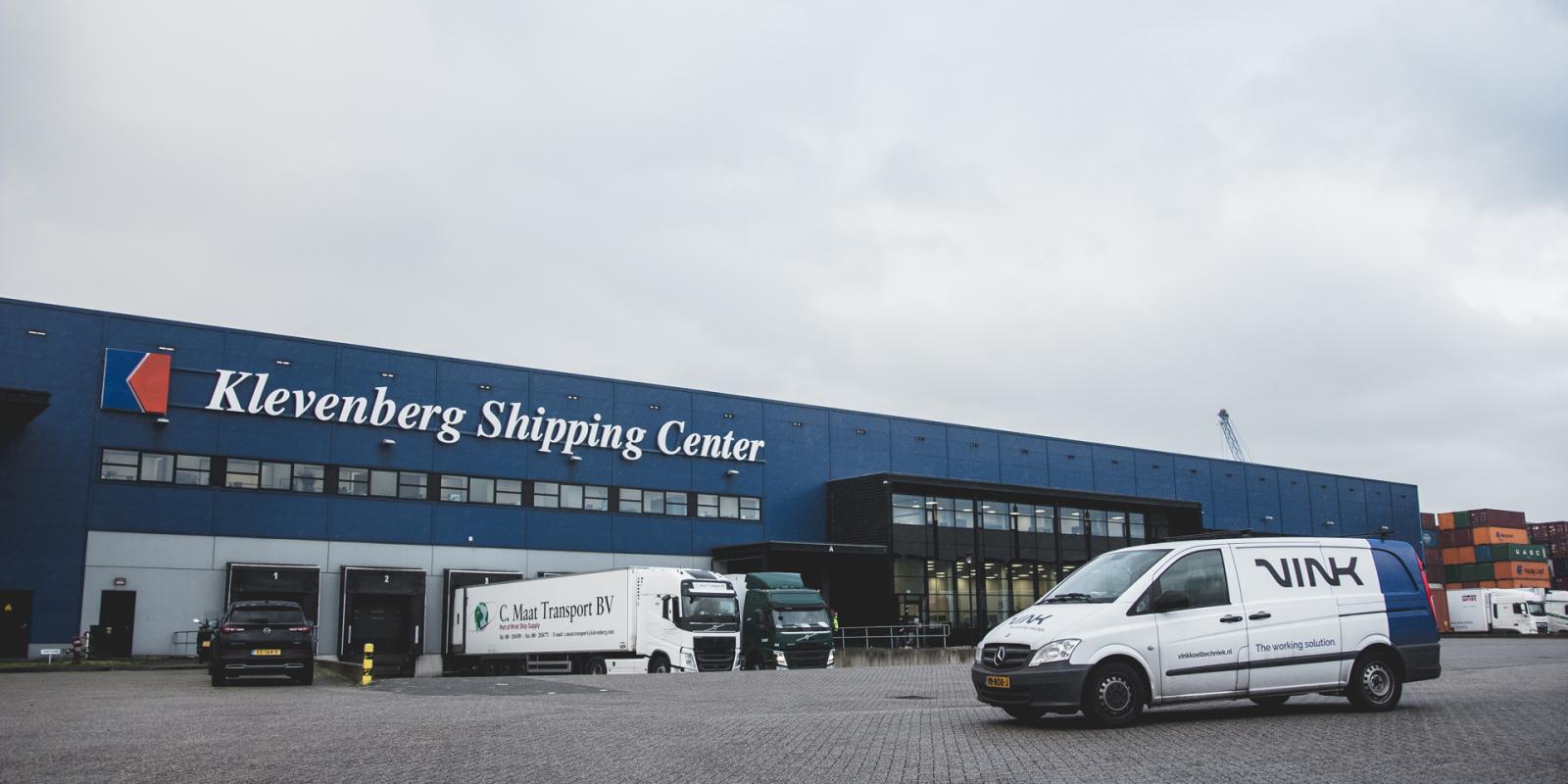
Ready for a sustainable upgrade? We'll design the solution for you
We love thinking about your organisation's future. We'll find you a sustainable solution that will last for years to come.